Osha’s stance on tool safety in the workplace emphasizes the importance of proper handling and use of tools to prevent accidents and injuries. Tool safety is a significant concern in the workplace, and it is crucial for employers and employees to adhere to OSHA’s guidelines.
OSHA, also known as the Occupational Safety and Health Administration, is a government agency that ensures safe and healthy working conditions for employees in the United States. OSHA’s stance on tool safety emphasizes that employers must provide appropriate training and personal protective equipment, and employees must follow safe work practices when using tools.
This includes proper handling, inspection, maintenance, and storage of tools to prevent accidents and injuries. By following OSHA’s guidelines, employers can create a safer work environment, reduce the risk of tool-related incidents, and protect the well-being of their employees.
Importance Of Osha Guidelines
OSHA guidelines play a crucial role in ensuring tool safety in the workplace. By setting standards and regulations, OSHA aims to protect workers from hazards and prevent accidents associated with tool usage. Compliance with OSHA guidelines is essential for maintaining a safe work environment and reducing the risk of injuries.
Tool safety in the workplace is of utmost importance to prevent accidents and promote a safe working environment. That’s where the Occupational Safety and Health Administration (OSHA) comes into play. OSHA has established guidelines and safety standards to ensure the proper use and maintenance of workplace tools.
Understanding the importance of adhering to these guidelines is crucial for both employers and employees. Let’s explore the significance of OSHA guidelines in promoting tool safety in the workplace.
Safety Standards For Workplace Tools:
- Inspections: OSHA guidelines mandate regular inspections of workplace tools to identify any faults, damage, or potential hazards. These inspections help to ensure that the tools are in proper working condition and free from defects that could jeopardize worker safety.
- Maintenance: Adhering to OSHA guidelines ensures that workplace tools are properly maintained. This includes regular cleaning, lubrication, and repair to keep them in optimal condition. Well-maintained tools reduce the risk of accidents and prolong their lifespan.
- Training: OSHA mandates that employees receive proper training on the safe handling and operation of tools. This includes providing instructions on how to use tools correctly, as well as precautions to take to avoid accidents. Such training equips employees with the necessary knowledge and skills to work safely with tools.
Osha’S Role In Ensuring Tool Safety:
- Enforcement: OSHA enforces compliance with tool safety guidelines by conducting regular inspections and issuing citations for violations. By holding employers accountable for ensuring tool safety, OSHA plays a crucial role in preventing accidents and promoting workplace safety.
- Guidance and assistance: OSHA provides guidance and assistance to employers and employees regarding the proper implementation of tool safety measures. This includes offering resources, training programs, and consultations to help workplaces establish effective tool safety protocols.
Benefits Of Complying With Osha Guidelines:
- Enhanced Safety: Complying with OSHA guidelines significantly reduces the risk of accidents and injuries in the workplace. Safe tools and proper handling practices create a safer working environment for everyone.
- Legal Compliance: Adhering to OSHA guidelines ensures that employers are in compliance with federal and state regulations. By complying with these regulations, businesses avoid legal repercussions and potential fines for non-compliance.
- Increased Productivity: When employees work with properly maintained tools that meet OSHA standards, they are less likely to experience interruptions due to tool failures or accidents. This leads to increased productivity and efficiency in the workplace.
By recognizing the importance of OSHA guidelines, organizations can establish a culture of safety, protect their employees, and ensure a productive and accident-free work environment. Adhering to these guidelines not only benefits the employees but also safeguards the employer from legal and financial liabilities.
Osha’S Definition Of A Safe Tool
OSHA defines a safe tool as one that meets specific safety requirements, ensuring workplace safety. Employers must comply with OSHA standards to protect workers from injuries caused by hazardous tools.
Tool safety is of paramount importance in the workplace to prevent accidents and ensure a safe working environment. OSHA, the Occupational Safety and Health Administration, has set specific criteria and guidelines for safe tool design, operation, and maintenance. By adhering to OSHA’s standards, employers can minimize the risk of injuries and create a safer workplace.
Let’s take a closer look at OSHA’s stance on tool safety and their definition of a safe tool.
Characteristics Of A Safe Tool:
- Ergonomic design: A safe tool should have an ergonomic design that reduces the strain on the user’s muscles and joints. Proper grip and handle shape, as well as the placement of controls, should be considered to minimize fatigue and enhance comfort during prolonged use.
- Durable construction: Tools should be made from high-quality materials that can withstand normal wear and tear. Proper construction ensures that tools will not break or malfunction during use, preventing accidents and injuries.
- Clear markings and labeling: Tools should have clearly visible markings and labels indicating their purpose, limitations, and any potential hazards associated with their use. This helps users select the right tool for the job and avoid misuse that could lead to accidents.
- Non-slip surfaces: Tools should have non-slip surfaces or handles to provide a secure grip, even in wet or slippery conditions. This feature prevents accidental slips and enhances user control during operation.
- Proper storage and maintenance: Safe tool storage and regular maintenance are essential to preserve their functionality and prevent accidents. Tools should be stored in designated places and inspected regularly for damage. Any damaged tools should be repaired or replaced promptly to avoid potential hazards.
Osha’S Criteria For Safe Tool Design:
- Guards and safety devices: Tools that have the potential to expose employees to hazards must be equipped with appropriate guards or safety devices. These devices are designed to prevent accidental contact with moving parts, sharp edges, or other potential sources of injury.
- Electrical safety: Tools powered by electricity should be designed with proper insulation and grounding to prevent electric shocks. Electrical cords should be in good condition, with no exposed wires or fraying.
- Noise and vibration reduction: Tools produce noise and vibration during operation which, if excessive, can lead to long-term health issues for the user. Safe tools should be designed to minimize noise levels and reduce vibration to acceptable limits.
- Proper weight and balance: Tools should be designed with consideration for their weight and balance to minimize fatigue and strain on the user. A well-balanced tool is easier to control and reduces the risk of accidents caused by fatigue-induced loss of control.
Ensuring Safe Tool Operation:
- Education and training: Employers should provide proper education and training to employees on the safe and correct operation of tools. This includes understanding the specific hazards associated with each tool and how to use and maintain them correctly.
- Regular inspections: Employers must conduct regular inspections of tools to identify any defects or issues that could compromise their safety. Inspections should be documented, and any identified problems should be addressed promptly.
- Reporting hazards: Employees should be encouraged to report any tool-related hazards or concerns to their supervisors. Establishing an open line of communication allows for prompt action and ensures a safer work environment.
- Prohibited use: Employers should clearly communicate any prohibited uses of tools to employees. This helps prevent misuse that may lead to accidents or injuries.
- Personal protective equipment (PPE): In situations where hazards cannot be eliminated, appropriate personal protective equipment, such as safety glasses, gloves, or hearing protection, should be provided to employees. This additional layer of protection helps prevent injuries while using tools.
By following OSHA’s criteria for safe tools, employers can create a workplace where tool-related accidents are minimized, promoting a safer and healthier environment for all employees. Adhering to these guidelines not only prevents unnecessary injuries but also demonstrates a commitment to employee well-being and compliance with OSHA regulations.
Osha Guidelines For Tool Maintenance
OSHA guidelines for tool maintenance are crucial in ensuring safety in the workplace. These guidelines outline the importance of regular inspections, proper storage, and maintenance of tools to prevent accidents and injuries. Complying with OSHA’s stance on tool safety is essential for creating a safe work environment.
Regular tool maintenance is crucial in maintaining a safe working environment. OSHA (Occupational Safety and Health Administration) has set guidelines to ensure the proper maintenance of tools in the workplace. Let’s examine the importance of regular tool maintenance, inspection and repair requirements, and employee training in tool maintenance.
Importance Of Regular Tool Maintenance
Maintaining tools in good condition offers several benefits, including:
- Increases tool efficiency and lifespan: Regular maintenance helps keep tools functioning at optimal levels, preventing breakdowns and extending their lifespan.
- Reduces the risk of accidents and injuries: Well-maintained tools are less likely to malfunction, reducing the risk of accidents and injuries in the workplace.
- Improves productivity: When tools are properly maintained, employees can work efficiently without interruptions caused by equipment failures.
- Saves costs: Repairing or replacing damaged tools can be costly. Regular maintenance can help identify issues early on, reducing expenses associated with major repairs or replacements.
Inspection And Repair Requirements
To ensure tools are in safe working condition, OSHA recommends the following inspection and repair requirements:
- Regular inspections: Tools should be inspected periodically to identify any signs of wear, damage, or malfunction. Inspections should be performed by trained personnel who can detect potential hazards and take appropriate actions.
- Routine cleaning: Tools should be cleaned regularly to remove dirt, debris, and other contaminants that may affect their functionality.
- Lubrication: Proper lubrication of tools, as recommended by manufacturers, helps prevent friction and corrosion, ensuring smooth operation.
- Repairs: Any damaged or faulty tools should be promptly repaired or replaced to maintain a safe working environment.
Training Employees On Proper Tool Maintenance
Providing adequate training to employees on proper tool maintenance is essential. Here’s why:
- Knowledge and awareness: Proper training ensures that employees are aware of the importance of tool maintenance and understand how it contributes to a safe work environment.
- Correct handling techniques: Training equips employees with the skills and knowledge needed to handle tools correctly, reducing the chances of damage or misuse.
- Inspection procedures: Employees should know how to conduct thorough inspections of tools to identify potential hazards or signs of wear.
- Reporting procedures: Employees should be trained on how to report any tool malfunctions, damages, or safety concerns to their supervisors.
In Summary
Tool maintenance plays a vital role in workplace safety. Following OSHA guidelines for regular maintenance, inspection, and repair of tools helps prevent accidents, improves productivity, and saves costs. Proper training of employees ensures that they understand the importance of tool maintenance and are equipped with the necessary skills to handle and inspect tools correctly.
By prioritizing tool maintenance, companies can create a safer work environment for their employees.
Osha’S Requirements For Personal Protective Equipment (Ppe)
OSHA requires employers to provide personal protective equipment (PPE) for tool safety in the workplace. This ensures that workers are protected from potential hazards and injuries while using tools. Compliance with OSHA’s PPE requirements is essential for maintaining a safe working environment.
Ensuring the safety of workers in the workplace is crucial, and OSHA (Occupational Safety and Health Administration) plays a vital role in setting guidelines for tool safety. One of the key aspects of these guidelines is the use of Personal Protective Equipment (PPE).
PPE refers to specialized gear and clothing designed to protect workers from potential hazards and injuries. OSHA requires employers to provide appropriate PPE and ensure its proper utilization. Let’s explore the types of PPE commonly used for tool safety and OSHA’s guidelines for their usage:
Types Of Ppe For Tool Safety:
- Eye and face protection: Safety glasses, goggles, and face shields shield the eyes and face from flying debris, sparks, and chemicals.
- Head protection: Hard hats safeguard against falling objects and head impacts.
- Hearing protection: Earmuffs and earplugs reduce the risk of hearing damage due to loud noise generated by power tools.
- Hand protection: Gloves protect against cuts, abrasions, and chemical exposure.
- Foot and leg protection: Steel-toe boots, metatarsal guards, and leg protectors shield the feet and legs from heavy objects, falling debris, and sharp tools.
- Respiratory protection: Respirators filter out harmful particles or chemicals in the air, preventing respiratory distress.
Osha’S Guidelines For Ppe Usage:
- Employers must conduct a workplace hazard assessment to identify potential risks and determine the necessary PPE.
- PPE should be provided to workers free of charge and be suitable for the hazards present in the specific work environment.
- Training on how to properly use, maintain, and inspect PPE should be provided to employees.
- PPE should be maintained in a clean and reliable condition, and any damaged or defective equipment should be replaced.
- Employees should be instructed to wear PPE whenever there is a risk of injury, and enforcement of this policy is essential.
Ensuring Proper Fit And Maintenance Of Ppe:
- Proper fit is crucial for effective protection. Employers must ensure that PPE fits each individual worker correctly and comfortably. Ill-fitting equipment may hinder movement or provide inadequate protection.
- Regular maintenance and inspection of PPE are necessary to identify any signs of wear, damage, or deterioration. This ensures ongoing protection and prevents potential accidents.
- Employees should be encouraged to report any issues or concerns regarding the fit or condition of their PPE, and prompt action should be taken to address these concerns.
Your workers’ safety is of utmost importance, and compliance with OSHA’s requirements for PPE usage is key in preventing workplace injuries. By providing the appropriate types of PPE, following guidelines, and ensuring proper fit and maintenance, you can create a safer working environment for your employees.
Osha Regulations For Tool Storage And Handling
OSHA regulations require employers to prioritize tool safety in the workplace. Proper storage and handling practices are necessary to prevent accidents and injuries. Compliance with these regulations ensures a safer work environment for employees.
**Safe practices for storing and securing tools**
When it comes to tool safety in the workplace, proper storage and securing techniques are crucial to prevent accidents and maintain a safe working environment. OSHA provides guidelines and regulations to help employers and employees maintain tool safety. Here are some safe practices for storing and securing tools:
- Store tools in designated areas: Establish specific areas or cabinets where tools can be safely stored when not in use. This helps minimize the risk of tools being misplaced or left in hazardous areas.
- Use tool organizers: Utilize tool organizers such as pegboards, toolboxes, or foam cutouts to keep tools neat, organized, and easily accessible. This helps prevent tools from falling, getting damaged, or causing injuries when reaching for them.
- Secure heavy or sharp tools: Tools that are heavy or have sharp edges should be properly secured to prevent them from falling or causing harm. Use racks, brackets, or specially designed holders to secure these types of tools.
- Implement a tool check-in/check-out system: Establish a system where employees are required to sign tools in and out, ensuring accountability and tracking of tool usage. This helps identify missing tools and promotes responsibility among employees.
- Regularly inspect and maintain storage areas: Regularly inspect storage areas to identify any damaged shelves, racks, or organizers. Repair or replace as necessary to ensure a safe and secure storage environment for tools.
**Preventing tool-related accidents during transportation**
Transporting tools safely is just as important as storing them properly. Accidents can occur if tools are not secured adequately during transportation. To prevent tool-related accidents during transportation, consider the following:
- Use secure toolboxes or containers: Invest in sturdy toolboxes or containers with secure latches or locks to transport tools. This helps prevent tools from shifting or falling out during transit.
- Use padding or cushioning materials: To protect fragile or sensitive tools, use padding materials such as foam or bubble wrap within the toolbox or container. This reduces the risk of damage to tools and protects them from unnecessary impacts.
- Secure tools within the vehicle: Ensure tools are secured within the vehicle to prevent them from moving or becoming dangerous projectiles in the event of sudden stops or accidents. Use straps, bungee cords, or cargo nets to secure toolboxes or containers in place.
**OSHA’s guidelines for handling tools safely**
OSHA emphasizes the importance of handling tools safely to prevent workplace injuries. Here are some of OSHA’s guidelines for handling tools safely:
- Inspect tools before use: Before using any tools, inspect them for any damage or defects. Replace or repair damaged tools to ensure safe working conditions.
- Use the right tool for the job: Select and use tools appropriate for the specific task at hand. Using the wrong tool can lead to accidents or reduce efficiency.
- Follow manufacturer instructions: Adhere to the manufacturer’s instructions for proper tool usage, maintenance, and storage. This helps ensure tools are used correctly and retain their functionality over time.
- Wear appropriate personal protective equipment (PPE): Always wear the necessary PPE, such as safety goggles, gloves, or hearing protection, when using tools. PPE safeguards against potential hazards and minimizes the risk of injury.
- Properly handle and grip tools: Use tools with a firm grip and handle them with care. Avoid using excessive force or applying pressure in unsafe manners that could lead to accidents.
By following these safe practices for storing, securing, transporting, and handling tools, employers and employees can create a safer work environment and reduce the risk of tool-related accidents in the workplace. Remember, tool safety is everyone’s responsibility.
Osha’S Recommended Training For Employees
OSHA emphasizes the importance of training employees in tool safety to ensure a safe work environment. With their recommended training programs, employees can learn proper handling and storage techniques, reducing the risk of accidents and injuries in the workplace.
Tool safety is a critical aspect of workplace safety, and ensuring employees receive proper training is essential to prevent accidents and injuries. OSHA, the Occupational Safety and Health Administration, has established guidelines and recommendations for tool-specific training programs. In this section, we will explore the importance of tool-specific training and OSHA’s guidelines for effective training programs.
Importance Of Tool-Specific Training:
- Tool-specific training is crucial to educate employees on the safe and correct use of tools in the workplace.
- Proper training helps employees understand potential hazards associated with various tools and how to mitigate them.
- It empowers workers to identify and report defective tools, reducing the risk of accidents.
- Training enhances employees’ skills and knowledge, leading to improved productivity and efficiency.
- By conducting tool-specific training, employers demonstrate their commitment to workplace safety, fostering a positive safety culture.
Osha’S Guidelines For Effective Training Programs:
- Customize training programs to address specific tool hazards and equipment used in the workplace.
- Provide a combination of hands-on training and theoretical instruction to ensure comprehensive learning.
- Train employees on the proper selection, inspection, and maintenance of tools to optimize their lifespan and prevent accidents.
- Incorporate training modules that cover safe handling, storage, and transportation of tools.
- Ensure training programs discuss emergency procedures, including the use of tools during emergency situations.
- Utilize qualified trainers with expertise in tool safety and keep the training materials up to date.
- Assess employees’ understanding through evaluations and provide feedback to reinforce learning.
- Regularly review and update training programs based on changing workplace conditions, equipment, or regulations.
Monitoring and reinforcing safe tool usage habits are equally important to sustain a safe working environment. Employers should establish processes to maintain ongoing compliance with the training provided, preventing complacency and promoting a safety-conscious workforce.
Enforcement And Consequences
Osha, the governing body for workplace safety, takes tool safety seriously by enforcing strict regulations. Non-compliance with these regulations can lead to severe consequences for both employers and employees. Safeguarding against accidents requires employers to prioritize tool safety and ensure proper training and equipment maintenance.
Osha Inspections And Penalties:
- OSHA conducts regular inspections to ensure compliance with tool safety regulations in the workplace.
- Inspectors evaluate the overall safety of tools, equipment, and work areas.
- Proper maintenance and training protocols are assessed during inspections.
- Non-compliance can result in penalties and citations.
Case Studies Of Companies Penalized For Tool Safety Violations:
- Company A: Received penalties for lack of training programs and inadequate maintenance of tools, leading to workplace accidents.
- Company B: Faced citations due to failure to provide proper personal protective equipment and inadequate safety protocols for tool usage.
Avoiding Legal And Financial Repercussions Through Compliance:
- Implement comprehensive and regular training programs on tool safety for employees.
- Establish proper maintenance schedules and inspections to ensure tools are in good working condition.
- Provide suitable personal protective equipment for employees using tools.
- Develop and enforce a robust safety policy that addresses tool handling procedures and protocols.
- Regularly review and update safety protocols to align with current industry standards.
By adhering to OSHA’s guidance on tool safety, companies can maintain a safe work environment, minimize the risk of accidents, and avoid the legal and financial consequences associated with non-compliance.
Osha’S Role In Promoting A Culture Of Safety
OSHA plays a crucial role in promoting a culture of safety in the workplace, including tool safety. By implementing regulations, conducting inspections, and providing training, OSHA ensures that employers prioritize the well-being of their workers and maintain a safe environment.
Compliance with OSHA guidelines helps prevent accidents and promotes a culture that values safety above all else.
Osha’S Outreach And Educational Programs
- OSHA understands the importance of tool safety in the workplace and plays a significant role in promoting a culture of safety. Through its outreach and educational programs, OSHA aims to ensure that employers and employees are aware of the regulations and best practices to maintain a safe working environment.
- These programs provide valuable resources and training materials that help employers create effective safety programs and educate employees on the proper use of tools. By equipping employers and employees with the necessary knowledge, OSHA strives to reduce accidents and injuries caused by tool-related incidents in the workplace.
Encouraging Proactive Safety Measures
- OSHA encourages proactive safety measures by emphasizing the importance of hazard identification and implementing preventive measures.
- By conducting regular inspections and audits, employers can identify potential hazards and take necessary actions to mitigate risks associated with tools.
- OSHA emphasizes the need for employers to involve employees in safety initiatives, encouraging them to report hazards and provide feedback on safety processes.
- By fostering a culture of proactive safety measures, OSHA aims to minimize workplace accidents and promote the well-being of employees.
Benefits Of Creating A Safe Work Environment
- Creating a safe work environment brings numerous benefits to both employers and employees. By prioritizing tool safety, employers can benefit from:
- Reduced worker injuries and illnesses, leading to decreased healthcare costs and workers’ compensation claims.
- Increased productivity and efficiency as employees work in a safe and secure environment.
- Enhanced company reputation and credibility, attracting skilled workers and potential clients who value safety initiatives.
- Compliance with OSHA regulations, minimizing the risk of penalties and legal consequences.
- Employees also enjoy several advantages when working in a safe environment:
- Peace of mind knowing that their well-being is a priority for their employer.
- Reduced risk of accidents and injuries, leading to improved physical and mental health.
- Increased job satisfaction and morale, resulting in higher productivity and engagement.
- Opportunities for growth and skill development through proper training and education on tool safety.
By understanding OSHA’s role in promoting a culture of safety, employers can prioritize tool safety, implement preventive measures, and create a safe work environment. Such efforts not only protect employees but also benefit employers by fostering productivity, reputation, and compliance with OSHA regulations.
Remember, tool safety is a shared responsibility that requires active participation from both employers and employees for a safe and thriving workplace.
Case Studies Of Successful Implementation Of Osha Guidelines
OSHAs stance on tool safety in the workplace is crucial for ensuring the well-being of employees. Through case studies of successful implementation, organizations can showcase how they have effectively adhered to OSHA guidelines, creating a safe working environment and reducing the risk of accidents or injuries.
This not only protects the employees but also demonstrates the company’s commitment to maintaining a healthy and secure workplace.
Examples Of Companies With Exemplary Tool Safety Practices:
- ABC Manufacturing: ABC Manufacturing has implemented OSHA’s tool safety guidelines diligently, resulting in a significant reduction in workplace incidents. They have designated trained employees to regularly inspect and maintain tools, ensuring they are in proper working condition. Additionally, ABC Manufacturing provides comprehensive training programs to employees, emphasizing the importance of using tools safely.
- XYZ Construction: XYZ Construction has taken a proactive approach to tool safety, implementing a comprehensive tool inspection process. Each tool is thoroughly examined before and after use, and any damaged or defective tools are immediately replaced. XYZ Construction also encourages open communication among employees regarding tool safety concerns and provides regular training sessions to reinforce safe tool usage.
Positive Impacts Of Following Osha’S Tool Safety Recommendations:
- Enhances employee safety: Following OSHA’s tool safety recommendations significantly reduces the risk of workplace incidents, protecting employees from potential injuries.
- Improves productivity: By adhering to OSHA’s tool safety guidelines, companies can minimize tool-related accidents and equipment failures, leading to uninterrupted workflow and increased productivity.
- Decreases financial losses: Implementing proper tool safety measures reduces the likelihood of workplace accidents, minimizing medical expenses, worker compensation claims, and potential legal penalties.
Lessons Learned From Successful Case Studies:
- Regular training and awareness: Successful companies prioritize ongoing training programs to ensure employees are aware of the latest tool safety practices. By regularly educating employees, companies can reinforce safe behaviors and prevent complacency.
- Effective communication: Open communication channels between management and employees foster a culture of safety. Encouraging employees to report tool safety concerns and addressing them promptly is crucial in preventing accidents.
- Robust inspection and maintenance procedures: Regular inspections of tools, machinery, and equipment can help detect any potential faults or hazards. Establishing maintenance protocols ensures tools are properly maintained and reduces the risk of accidents caused by malfunctioning equipment.
Remember, implementing OSHA’s tool safety recommendations not only protects employees but also enhances productivity and minimizes financial losses. By following the examples set by companies with exemplary tool safety practices, businesses can create a safer work environment for everyone involved.
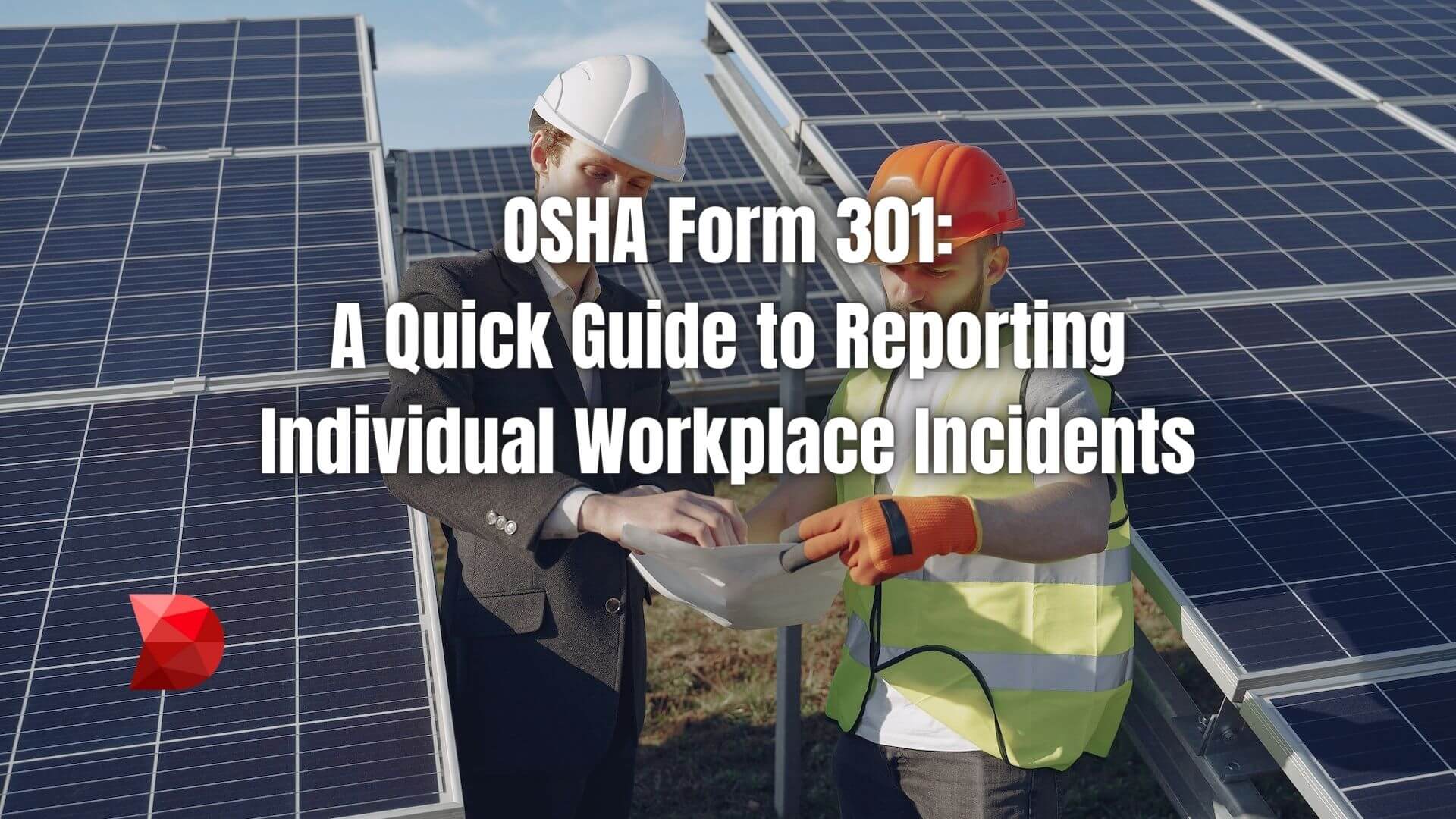
Credit: datamyte.com
Osha’S Collaboration With Employers And Employees
OSHA ensures workplace tool safety through collaboration with employers and employees, emphasizing the importance of preventive measures and proper training. This partnership helps create a safe and secure work environment, reducing the risk of accidents and injuries.
In order to ensure tool safety in the workplace, OSHA emphasizes the importance of collaboration between employers and employees. By working together, they can create a culture of safety and prevent accidents. Let’s delve into the roles and responsibilities of both employers and employees, OSHA’s partnership programs, and the benefits of open communication and collaboration.
Roles And Responsibilities Of Both Employers And Employees:
- Employers have the primary responsibility of providing a safe and healthy work environment for their employees. This includes implementing effective safety programs and policies to prevent tool-related incidents.
- Employers should conduct regular inspections to identify any hazards and promptly address them to avoid potential accidents.
- Employers should also provide the necessary training to employees regarding proper tool handling, maintenance, and storage.
- Employees, on the other hand, are responsible for adhering to the safety protocols established by their employers.
- They should use tools only for their intended purposes and report any damaged or faulty tools to their supervisors.
- Employees should also take an active role in maintaining a clean and organized work environment to reduce the risk of accidents.
Osha’S Partnership Programs For Improved Safety:
- OSHA encourages employers and employees to participate in partnership programs that focus on improving safety in the workplace.
- These programs provide a platform for collaboration, allowing both parties to share best practices and learn from each other’s experiences.
- Through partnerships, employers and employees can work together to identify and address potential safety hazards.
- OSHA’s Strategic Partnership Program (SPP) and the Voluntary Protection Programs (VPP) are examples of initiatives that foster collaboration between OSHA, employers, and employees to promote workplace safety.
Benefits Of Open Communication And Collaboration:
- Open communication between employers and employees plays a crucial role in ensuring tool safety in the workplace.
- When employees feel comfortable reporting potential hazards or suggesting improvements, it creates a proactive safety culture.
- Collaboration allows for the identification and implementation of effective safety measures that address specific risks in the workplace.
- By working together, both employers and employees can contribute to the development and enforcement of comprehensive tool safety procedures.
- Open communication and collaboration also enhance employee engagement and morale, leading to a more productive and safer work environment.
OSHA emphasizes collaboration between employers and employees to achieve tool safety in the workplace. By understanding their roles and responsibilities, participating in partnership programs, and fostering open communication and collaboration, employers and employees can work together towards creating a safe and secure work environment.
Remember, safety is a shared responsibility that requires the active involvement of all stakeholders.
Frequently Asked Questions On What Is Osha’S Stance On Tool Safety In The Workplace?
What Is The Osha Regulation Code Regarding Tool Safety?
OSHA regulation code for tool safety is essential for maintaining a safe work environment.
Does Osha Regulate Hand And Power Tool Safety?
Yes, OSHA regulates hand and power tool safety to ensure workplace safety standards are met.
What Is Osha’S Role In The Workplace Safety?
OSHA ensures workplace safety by setting and enforcing standards to protect workers from hazards.
What Are The 7 General Guidelines For Workplace Safety As Recommended By Osha?
OSHA recommends 7 general guidelines for workplace safety. They are: 1. Provide a safe and healthy work environment. 2. Use safety equipment and proper tools. 3. Implement hazard communication. 4. Conduct training and education programs. 5. Establish emergency response procedures.
6. Encourage employee involvement in safety initiatives. 7. Regularly monitor and evaluate safety performance.
Conclusion
Overall, it is clear that OSHA places a heavy emphasis on tool safety in the workplace. By providing guidelines and regulations, OSHA aims to protect workers from the potential hazards associated with tools. Compliance with these safety standards not only ensures the well-being of employees, but also minimizes the risk of accidents, injuries, and financial losses for employers.
Employers play a critical role in maintaining a safe work environment by implementing appropriate safety protocols, providing training to workers, regularly inspecting tools, and addressing any issues promptly. In addition, employees must also take responsibility for using tools correctly, reporting any unsafe conditions, and actively participating in safety programs.
By prioritizing tool safety, organizations can foster a culture of safety, foster a positive work environment, and ultimately contribute to the overall success and well-being of their workforce.