Maintaining power tools can involve common issues such as motor malfunctions and faulty wiring. Power tools may experience problems with their motors or wiring, which can affect their performance.
These issues can hinder the tool’s functionality and pose safety risks to the user. Proper maintenance is necessary to address these concerns and ensure the tools are in working order. By addressing motor malfunctions and faulty wiring promptly, users can enjoy the full benefits of their power tools and reduce the risk of accidents or injuries.
Understanding The Importance Of Power Tool Maintenance
Proper maintenance of power tools is crucial to ensure their longevity and optimal performance. However, users often encounter common issues such as motor problems, worn-out brushes, and faulty switches when maintaining power tools. Regular inspections and servicing can help prevent these issues and extend the lifespan of power tools.
Significance Of Regular Power Tool Maintenance
Power tools are essential for performing various tasks, whether it’s for DIY projects or professional work. However, many people overlook the importance of regular maintenance for their power tools. Understanding the significance of power tool maintenance can help you prolong their lifespan and ensure optimum performance.
Let’s explore why regular maintenance is crucial:
- Preventing breakdowns and malfunctions: Regular maintenance helps identify and address any potential issues with your power tools before they turn into major problems. By inspecting and servicing your tools regularly, you can catch small issues early on and prevent breakdowns or malfunctions during crucial tasks.
- Enhancing safety: Well-maintained power tools are safer to use. Regular maintenance allows you to identify any safety hazards, such as loose parts, frayed cords, or worn-out components. By addressing these issues promptly, you can reduce the risk of accidents or injuries while using your power tools.
- Improving efficiency and performance: Neglected power tools tend to lose their efficiency and performance over time. Regular maintenance ensures that your tools are operating at their optimal level. This includes cleaning or replacing filters, lubricating moving parts, and checking for proper calibration. By keeping your power tools in top-notch condition, you can accomplish tasks more efficiently and achieve better results.
- Cost savings: Proper maintenance can save you money in the long run. By investing a little time and effort in maintaining your power tools, you can prevent major breakdowns that may require expensive repairs or even tool replacements. Regular maintenance helps extend the lifespan of your tools, allowing you to maximize your investment.
- Preserving warranty coverage: Most power tools come with manufacturer warranties that require regular maintenance to remain valid. Failure to adhere to the recommended maintenance schedule may void your warranty. By following the maintenance guidelines, you can preserve your warranty coverage and ensure easy access to repairs or replacements if needed.
Regular power tool maintenance offers a range of benefits: preventing breakdowns, enhancing safety, improving performance, saving costs, and preserving warranty coverage. Make it a habit to include maintenance tasks in your tool care routine, and you’ll enjoy the long-lasting performance and reliability of your power tools.
Identifying Common Issues In Power Tool Maintenance
When maintaining power tools, it is important to identify common issues that may arise. These issues can include motor malfunctions, worn-out brushes, loose or damaged parts, overheating, and dull blades or bits. Regular inspection and proper maintenance can help extend the lifespan of power tools and ensure optimal performance.
Power tools are essential for completing various tasks efficiently, but they require regular maintenance to ensure optimal functionality and longevity. Understanding the common issues that can arise during power tool maintenance is crucial for addressing them promptly. Here are some key issues to look out for:
Overheating And Temperature Management:
Power tools generate a significant amount of heat during use, and it’s important to manage temperature levels to prevent overheating. Here are a few points to consider:
- Inadequate airflow: Insufficient ventilation can lead to overheating. Ensure that the tool’s cooling vents are clean and free from dust and debris.
- Extended use without breaks: Prolonged use without giving the tool a break can cause overheating. Allow the tool to cool down periodically during extended operation.
- Excessive strain on the motor: Pushing the tool beyond its capacity can generate excessive heat. Be mindful of the tool’s limitations and avoid overloading it.
Lubrication And Friction-Related Problems:
Proper lubrication is essential for smooth operation and to reduce wear and tear. Friction-related issues can cause power tools to malfunction. Consider the following:
- Insufficient lubrication: Inadequate or improper lubrication can lead to excessive friction, resulting in decreased performance. Regularly lubricate moving parts as recommended by the manufacturer.
- Dry or dirty gears: Gears play a vital role in power tool functionality. Ensure that they are adequately lubricated and free from dust and debris to prevent damage and ensure smooth operation.
- Worn-out bearings: Bearings facilitate smooth movement and reduce friction. Regularly check and replace worn-out bearings to avoid performance issues.
Dust And Debris Accumulation In Tool Components:
During use, power tools can accumulate dust and debris, which can hinder their performance and lead to malfunctions. Here are some considerations:
- Clogged air filters: Dust and debris can clog the air filters of power tools, restricting airflow. Clean or replace air filters regularly to prevent overheating and maintain optimal performance.
- Jammed vents and cooling systems: Blocked vents and cooling systems can impair heat dissipation, causing overheating. Keep these areas clean to prevent malfunctions.
- Contaminated switches and controls: Dust and debris can interfere with the proper functioning of switches and controls. Clean these components regularly to avoid operational issues.
By familiarizing yourself with these common issues in power tool maintenance, you can take appropriate actions to address problems promptly, ensuring the longevity and optimal performance of your power tools.
Overheating: Causes And Prevention
Power tools are prone to overheating, which can lead to common issues such as reduced performance and potential damage. To prevent overheating, it’s crucial to ensure proper ventilation, avoid overworking the tool, and regularly clean and maintain the tool’s components.
Importance Of Proper Usage Intervals
Proper usage intervals play a crucial role in maintaining power tools and preventing overheating. By following recommended guidelines, you can ensure that your tools perform optimally and have a longer lifespan. Here are some key points to keep in mind:
- Use power tools for the designated tasks only: Each power tool is designed for specific applications. It is important to avoid using a tool for tasks that it is not intended for, as this can put unnecessary strain on the motor and cause overheating.
- Take breaks during prolonged use: Continuous operation of power tools can cause excessive heat buildup. To prevent overheating, it is important to take regular breaks during extended periods of use. This allows the tool to cool down and reduces the risk of damage.
- Follow manufacturer’s instructions for duty cycles: Power tool manufacturers often provide recommended duty cycles, which specify the maximum continuous use time for a tool before it needs to cool down. It is essential to adhere to these instructions as they are tailored to each tool’s specific capabilities.
Ensuring Adequate Ventilation During Tool Operation
Proper ventilation is essential to prevent overheating in power tools. Insufficient airflow can lead to the accumulation of heat, causing the tool to malfunction or fail prematurely. Here are some practices to ensure adequate ventilation during tool operation:
- Keep air vents clear: Power tools often have built-in air vents to allow for air circulation and cooling. It is important to regularly clean and remove any obstructions from these vents to prevent heat buildup.
- Maintain proper clearance: When using power tools, make sure there is sufficient clearance around the tool to allow air to flow freely. Avoid using the tool in tight or cramped spaces where airflow may be restricted.
- Use tools in well-ventilated areas: Operating power tools in poorly ventilated areas can exacerbate heat buildup. Whenever possible, use tools in well-ventilated spaces or consider using additional ventilation equipment, such as fans or air extractors.
Monitoring Heat Levels And Using Cooling Mechanisms
To avoid overheating, it is crucial to monitor the heat levels of power tools and employ cooling mechanisms when necessary. Here are some steps to help you effectively manage heat levels:
- Regularly check the tool’s temperature: During use, regularly touch the tool to assess its temperature. If it feels excessively hot to the touch, it may be overheating. In such cases, discontinue use and allow the tool to cool down.
- Utilize cooling periods: Some power tools feature thermal shut-off mechanisms designed to protect against overheating. If your tool has this feature, ensure that you allow it to cool down during the recommended intervals.
- Use cooling aids: In situations where extended tool use is required, consider using cooling aids such as compressed air or cooling sprays. These can help dissipate heat and maintain a safe operating temperature.
By following these guidelines and incorporating proper maintenance practices, you can greatly reduce the risk of overheating in your power tools. Remember, prevention is key to ensuring optimal tool performance and longevity.
Lubrication: Choosing The Right Lubricants
Choosing the right lubricants for power tools is crucial in maintaining their performance. Common issues can include inadequate lubrication causing increased friction and wear, improper lubricant selection leading to residue buildup, and using incompatible lubricants resulting in damage to the power tools.
Understanding the specific lubrication requirements of each tool and using the recommended lubricants can help prevent these issues and ensure optimal tool performance and longevity.
Understanding The Types Of Lubricants For Power Tools:
Choosing the right lubricant for your power tools is essential in maintaining their performance and longevity. There are different types of lubricants available, each designed for specific parts and applications. Understanding these lubricant options will help you make informed decisions and keep your power tools in excellent condition.
- Grease: Grease is a semi-solid lubricant that offers excellent resistance to moisture and provides long-lasting lubrication. It is commonly used for heavy-duty applications and parts that endure high pressure and temperature. Grease forms a protective barrier that prevents metal-to-metal contact and reduces friction.
- Oil: Oil is a liquid lubricant that is ideal for most power tool applications. It flows easily into hard-to-reach areas and provides excellent lubrication for moving parts. Oil comes in different viscosities to suit various power tool types. It is essential to choose the right oil viscosity to ensure proper lubrication and prevent excessive wear and tear.
- Dry Lubricants: Dry lubricants, such as graphite or silicone spray, offer an alternative to traditional greases and oils. These lubricants do not attract dirt or dust, making them suitable for applications where cleanliness is crucial. Dry lubricants are commonly used for tools with plastic or rubber parts, as they do not cause damage or degradation.
Importance Of Lubricating Moving Parts Regularly:
Regular lubrication of power tool moving parts is crucial for their optimal performance and longevity. Failure to do so can lead to increased friction, wear, and potential damage. Here are some reasons why regular lubrication is essential:
- Reduced Friction: Lubrication reduces the friction between moving parts, allowing them to operate smoothly. This helps prevent excessive heat buildup and minimizes wear on the tool components.
- Prevention of Wear and Tear: By lubricating regularly, you can prevent premature wear and tear on important power tool components, such as bearings, gears, and joints. Lubricants create a barrier that reduces metal-to-metal contact and protects against corrosion.
- Improved Efficiency: Proper lubrication ensures that power tools operate at their optimum efficiency level. With less friction and smoother movement, tools can deliver their full power, resulting in improved performance and productivity.
Tips For Proper Lubrication Techniques:
Proper lubrication techniques are vital to ensure effective lubrication and to maximize the lifespan of your power tools. Follow these tips to lubricate your power tools correctly:
- Refer to the Manufacturer’s Guidelines: Always consult the manufacturer’s guidelines or user manual for recommended lubricants and lubrication intervals specific to your power tools. Following these instructions will help you maintain the tool’s warranty and ensure optimal performance.
- Clean and Inspect: Before lubricating, clean the surfaces and parts that require lubrication. Remove any dirt, debris, or old lubricant to ensure the new lubricant can penetrate effectively. Additionally, inspect for any signs of damage or wear that may require maintenance or replacement.
- Apply the Right Amount: Applying the correct amount of lubricant is crucial. Applying too little may result in inadequate lubrication, while applying too much can lead to excess buildup and attract more dirt and debris. Apply the lubricant according to the manufacturer’s recommendations.
- Apply in the Right Areas: Identify the specific areas that require lubrication based on the manufacturer’s guidelines. Power tools have various moving parts, such as gears, bearings, and joints, which need lubrication. Apply the lubricant precisely to these areas to ensure optimal performance.
- Regular Maintenance Schedule: Establish a regular maintenance schedule for lubrication to ensure your power tools receive consistent attention. This will help prevent any potential issues caused by insufficient lubrication and promote longer tool lifespan.
Proper lubrication is a fundamental aspect of power tool maintenance. Understanding the types of lubricants available, the importance of regular lubrication, and implementing proper lubrication techniques will help you keep your power tools running smoothly and efficiently.
Dealing With Dust And Debris Accumulation
Maintaining power tools can be challenging due to the accumulation of dust and debris, leading to common issues like reduced efficiency and increased wear and tear. Regular cleaning and proper storage can help prevent these problems and ensure the longevity of your power tools.
Importance Of Cleaning Power Tools After Use
Maintaining power tools involves addressing various issues to ensure optimal performance and longevity. One common challenge faced by tool owners is dealing with dust and debris accumulation. Proper cleaning is crucial for several reasons:
- Prolonged Tool Life: Dust and debris can gradually wear down power tools, affecting their functionality and reducing their lifespan. Regularly cleaning the tools removes contaminants that may cause damage over time.
- Enhanced Performance: Accumulated dust and debris can hinder the performance of power tools, leading to decreased efficiency and effectiveness. Cleaning the tools ensures that they operate at their maximum potential.
- Safety Precaution: Dust particles can be hazardous to both the tool operator and anyone nearby. Inhalation of fine dust can cause respiratory issues, while debris on surfaces can increase slip and fall risks. Thoroughly cleaning power tools eliminates these safety hazards.
To effectively address dust and debris accumulation, consider following these tips:
Choosing The Right Cleaning Tools And Techniques
- Compressed Air: Using compressed air is a quick and efficient method to remove loose dust and debris from power tools. Ensure that the air pressure is appropriate for the tool being cleaned to avoid causing any damage.
- Soft Bristle Brush: A soft bristle brush, such as a paintbrush or toothbrush, can help tackle dust and debris in hard-to-reach areas. Gently brushing away accumulated dirt ensures thorough cleaning without scratching or harming the tool’s surface.
- Damp Cloth: Wiping down power tools with a damp cloth can effectively remove stubborn dirt and grime. Ensure that the cloth is slightly damp, not wet, to prevent water damage to electrical components.
Ensuring Dust Extraction Systems Are Operating Effectively
- Check and Clean Filters: If your power tool is equipped with a dust extraction system, regularly inspect and clean the filters. Clogged filters reduce the system’s efficiency and may lead to dust and debris buildup inside the tool.
- Verify Hose Connections: Ensure that the dust extraction hose is securely attached to the power tool and the vacuum or dust collection system. Loose connections can result in ineffective dust extraction and increased accumulation on surfaces.
- Regular Maintenance: Periodically inspect the entire dust extraction system, including hoses, fittings, and vacuum units, to ensure they are working correctly. Schedule routine maintenance as necessary to prevent malfunctions and ensure optimal performance.
Maintaining power tools is essential for their longevity, performance, and user safety. By prioritizing proper cleaning techniques, choosing suitable tools, and ensuring effective dust extraction systems, you can extend the lifespan of your power tools and enjoy their optimal functionality.
Maintaining The Power Supply
Maintaining power tools can pose common issues such as overheating, worn-out parts, power fluctuations, and improper maintenance. It’s important to address these concerns to ensure a consistent and uninterrupted power supply.
Ensuring that power tools have a reliable and efficient power supply is essential for their proper functioning and longevity. Neglecting power supply maintenance can lead to various issues, including electrical malfunctions and decreased productivity. Here are some important steps to consider when maintaining the power supply of your tools:
- Checking power cords and connections regularly: Power cords are prone to wear and tear, which can compromise their safety and functionality. Regularly inspect the power cords for any signs of fraying or damage. It’s crucial to address any issues promptly by fixing or replacing damaged cords. Additionally, ensure that the power connections are secure and free of debris or dirt that may impede proper power supply.
- Ensuring proper voltage and amperage for the tool: Power tools have specific voltage and amperage requirements for optimal performance. Using incorrect voltage or amperage can not only affect the tool’s functionality but also pose safety hazards. It’s vital to consult the user manual or manufacturer guidelines to determine the correct voltage and amperage for your power tool. Using a voltage meter or ammeter can help verify if the power supply meets the tool’s requirements.
- Identifying and addressing electrical issues promptly: Power tools can encounter electrical problems over time, such as short circuits or ground faults. These issues can lead to frequent tripping of breakers, inconsistent power supply, or even tool damage. If you notice any abnormal behavior, such as unusual noises, sparks, or variations in power output, it’s crucial to address them promptly. Consult a qualified electrician if needed to diagnose and fix electrical issues to prevent further damage to the tool or potential accidents.
Maintaining a reliable power supply for your power tools is crucial for their proper functioning and durability. Regularly checking power cords and connections, ensuring proper voltage and amperage, and addressing electrical issues promptly will help keep your tools running smoothly and prolong their lifespan.
Remember to prioritize safety and consult professionals when necessary.
Battery Maintenance: Maximizing Performance
Maximizing the performance of power tools involves addressing common battery maintenance issues. By identifying and addressing issues like overcharging, temperature extremes, and insufficient charging, users can optimize the lifespan and functionality of their power tool batteries.
Understanding Battery Types And Maintenance Requirements
- Lithium-ion batteries: These are commonly used in power tools due to their high energy density and long-lasting performance. They require minimal maintenance but should be charged before completely draining to maximize their lifespan.
- Nickel-based batteries: These include nickel-cadmium (NiCd) and nickel-metal hydride (NiMH) batteries. NiCd batteries are known for their durability but suffer from memory effect if not fully discharged before recharging. NiMH batteries have a higher capacity but are less prone to memory effect. Both types benefit from regular deep discharge and recharge cycles.
- Lead-acid batteries: These are typically found in larger power tools. Regular maintenance includes checking the electrolyte levels, ensuring proper ventilation, and maintaining a full charge to prevent sulfation.
Proper Charging And Storage Techniques
- Charge batteries at room temperature: Avoid charging batteries in extreme temperatures as it can affect their performance and lifespan.
- Use the right charger: Always use the charger specifically designed for the type of battery being charged. Using the wrong charger can lead to overcharging or undercharging.
- Avoid overcharging: Once a battery is fully charged, disconnect it from the charger to prevent overcharging, which can reduce its lifespan.
- Store batteries properly: Keep batteries in a cool and dry place, away from direct sunlight and extreme temperatures. If possible, store batteries at around 40% charge to maintain optimal performance.
- Maintain cleanliness: Ensure that battery contacts are clean and free from dirt or corrosion to ensure a good connection.
Troubleshooting Common Battery-Related Problems
- Inspect for damage: If a power tool is not functioning properly, check the battery for any visible signs of damage or corrosion. This could indicate a faulty battery that needs to be replaced.
- Check connections: Make sure the battery is securely connected to the power tool. Loose or dirty connections can lead to poor performance or no power at all.
- Reset the battery: Some batteries have a reset button or function to troubleshoot issues. Refer to the manufacturer’s instructions to perform a reset if necessary.
- Test with another battery: If possible, try using a different battery to see if the issue lies with the battery or the power tool itself.
- Seek professional help: If troubleshooting steps don’t resolve the issue, it’s best to consult a professional or contact the manufacturer for further assistance.
Routine Inspection And Calibration
Routine inspection and calibration are essential for maintaining power tools. Some common issues to watch out for include wear and tear, loose screws or bolts, damaged cords, and misaligned components. Regular checks can prevent accidents and ensure optimal tool performance.
Regular Inspection Of Power Tool Components:
- The first step in maintaining power tools is to regularly inspect their components.
- Inspecting power tool components helps identify any issues that might affect the tool’s performance and safety.
- Here are some key components to inspect:
- Power cords: Check for any signs of damage, such as fraying or exposed wires.
- Plugs and outlets: Ensure they are clean, proper fitting, and not loose.
- Housing and handles: Look for cracks, chips, or excessive wear that may impair functionality or grip.
- Cutting edges: Examine blades, bits, or cutting surfaces for dullness, damage, or missing teeth.
- Fasteners: Tighten or replace any loose or damaged screws, bolts, or nuts.
- Safety features: Verify that guards, shields, or safety switches are in place and working correctly.
- Dust collection systems: Clean or replace filters and suction tubes to maintain efficient dust removal.
- Moving parts: Lubricate gears, bearings, or moving mechanisms as per manufacturer’s instructions.
Regular inspection of these power tool components can help prevent accidents, ensure optimal performance, and prolong the lifespan of the tools.
Proper Storage And Transportation
Maintaining power tools can be challenging, with common issues arising from improper storage and transportation. These may include rusting, damage due to improper handling, and loss of parts or accessories. Proper care and attention to storage and transport can help extend the lifespan and functionality of power tools.
Importance Of Proper Storage To Prevent Damage:
- Storing power tools in a proper manner is essential to prevent damage and prolong their lifespan. Failure to do so can result in costly repairs or even the need for replacement. Here’s why proper storage is important:
Tips For Organizing And Protecting Power Tools:
- Keeping power tools organized not only makes it easier to find and access them when needed, but also helps to protect them from damage. Here are some tips for organizing and protecting your power tools:
- Use toolboxes or storage cases: Invest in sturdy toolboxes or storage cases specifically designed for power tools. These will provide a safe and secure place to store your tools, protecting them from dust, moisture, and accidental damage.
- Utilize foam inserts or custom organizers: Consider using foam inserts or custom organizers within your toolboxes or storage cases. These can be tailored to fit each tool, creating individual compartments and providing extra protection against scratches and shocks.
- Label and arrange your tools: Labeling your tools and arranging them systematically in your storage area or toolbox can save you time and effort when searching for a specific tool. It also reduces the risk of accidentally mishandling or damaging other tools.
- Regularly clean and maintain your tools: Dust and debris can accumulate on power tools, leading to performance issues or premature wear. Regularly clean your tools to remove dirt and debris, and inspect them for any signs of damage or wear.
Safe Practices For Transporting Power Tools:
- Whether you are moving your tools to another worksite or storing them away after a job, proper transportation is crucial to prevent damage and ensure safety. Here are some safe practices to follow when transporting power tools:
- Secure your tools properly: Make sure your power tools are securely packed and fastened down during transportation. This prevents them from shifting or falling, reducing the risk of damage and potential injuries.
- Protect against impacts: Wrap your power tools in soft materials, such as towels or bubble wrap, before placing them in a storage bag or toolbox. This provides an extra layer of protection against impacts during transit.
- Avoid leaving tools unattended: Never leave power tools unattended while they are being transported. This reduces the risk of theft and accidental damage.
- Follow manufacturer’s instructions: Always follow the manufacturer’s instructions for transporting specific power tools. They may provide additional guidance on securing and protecting the tools during transportation.
Remember, properly storing and transporting your power tools not only protects your investment but also ensures their safe and efficient use. By implementing these tips and practices, you can avoid common issues and enjoy the longevity of your power tools.
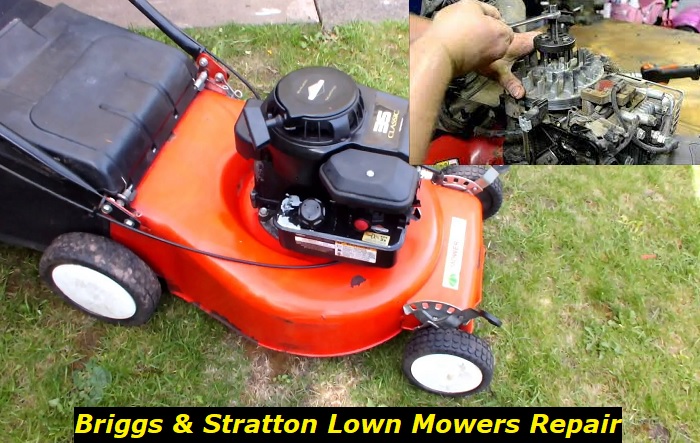
Credit: speceps.com
Professional Servicing And Repairs
Common issues when maintaining power tools include motor malfunctions, worn-out brushes, overheating, broken cords, or blunt blades. Ensuring regular servicing and repairs can prevent these problems and keep your power tools in optimal condition for efficient performance. Trust professionals to address any power tool issues promptly.
Recognizing When Professional Help Is Needed
- When power tools start showing signs of malfunction, it is important to assess whether the issue can be resolved on your own or if professional help is required. Here are some instances where seeking professional assistance becomes necessary:
- If the power tool is emitting strange sounds or vibrations that are not typical of its normal operation.
- When the power tool fails to start or experiences intermittent power loss.
- If there is a sudden decrease in performance or power output of the tool.
- When the tool’s safety features, such as the safety switch or blade guard, are not functioning properly.
- If there are visible damage or wear to critical components of the power tool.
- When troubleshooting attempts fail to resolve the issue and the problem persists.
Choosing A Reputable Service Center Or Technician
It is crucial to find a reliable service center or technician to ensure that your power tool is handled by qualified professionals. Here’s what to consider when choosing a service center or technician:
- Check for certifications or accreditations that indicate the expertise and knowledge of the service provider.
- Read customer reviews and testimonials to gauge the reputation and quality of the service center or technician.
- Inquire about the warranty and guarantee for the repair work performed.
- Ensure that the service center has experience working with the specific brand and model of your power tool.
- Consider the location and convenience of the service center, especially if you need to drop off or pick up your power tool.
- Compare the pricing and turnaround time offered by different service centers, while keeping quality and expertise in mind.
Scheduling Regular Servicing And Repairs
Regular servicing and repairs are essential to maintaining the performance and lifespan of your power tools. Consider the following when scheduling servicing and repairs:
- Follow the manufacturer’s guidelines for maintenance intervals and recommended servicing.
- Keep a record of the dates and types of servicing performed on each power tool to track their maintenance history.
- Schedule servicing during periods of low tool usage or downtime to minimize disruption to your work.
- Be proactive in addressing minor issues before they worsen and cause more significant damage to the power tool.
- Plan for regular inspections and cleanings to prevent dust, debris, or foreign objects from impacting the tool’s functionality.
- Be mindful of any specific service or repair requirements for different power tool types, such as batteries for cordless tools.
Regular servicing and repairs not only ensure optimal performance but also prolong the lifespan of your power tools, ultimately saving you time and money in the long run.
Frequently Asked Questions On What Are Some Common Issues When Maintaining Power Tools?
What Are The Common Problems Of Power Tools?
Common problems with power tools include overheating, motor issues, dull blades, and electrical malfunctions.
What Are 5 Risks Associated With Power Tools?
Using power tools carries the following 5 risks: electrocution, cuts and lacerations, falls and slips, flying debris, and hearing damage.
How Do You Maintain Power Tools?
To maintain power tools: 1. Clean and lubricate regularly to prevent dirt buildup and ensure smooth operation. 2. Check and replace worn or damaged parts promptly for safety and optimal performance. 3. Store in a dry and secure place to prevent rust and unauthorized access.
4. Follow manufacturer’s guidelines for maintenance and usage to extend the tool’s lifespan.
What Are The 7 Main Factors To Be Considered When Using A Power Tool?
Here are the 7 main factors to consider when using a power tool: safety precautions, proper maintenance, correct usage, suitable accessories, power source compatibility, ergonomics, and noise level control.
Conclusion
Maintaining power tools can be a challenging task, but by being aware of the common issues that may arise, individuals can take proactive steps to prevent or address them. Regularly inspecting tools for wear and tear, cleaning them after use, and storing them properly can help extend their lifespan and effectiveness.
Additionally, following manufacturer guidelines for maintenance, such as replacing worn-out parts and lubricating moving components, is crucial for optimal performance. It is also essential to monitor power tool performance and identify any unusual sounds, vibrations, or overheating, as these may be indications of underlying issues that need attention.
By staying proactive, power tool users can minimize downtime, increase productivity, and ensure the longevity of their equipment. So, whether you are a professional tradesperson or a DIY enthusiast, prioritizing power tool maintenance is key to getting the most out of your tools and keeping them in top-notch condition.